TUnIS Navigation MT
TUnIS Navigation MT is the world’s first and only microtunnelling navigation platform that combines all common and proven navigation technologies in one product line.

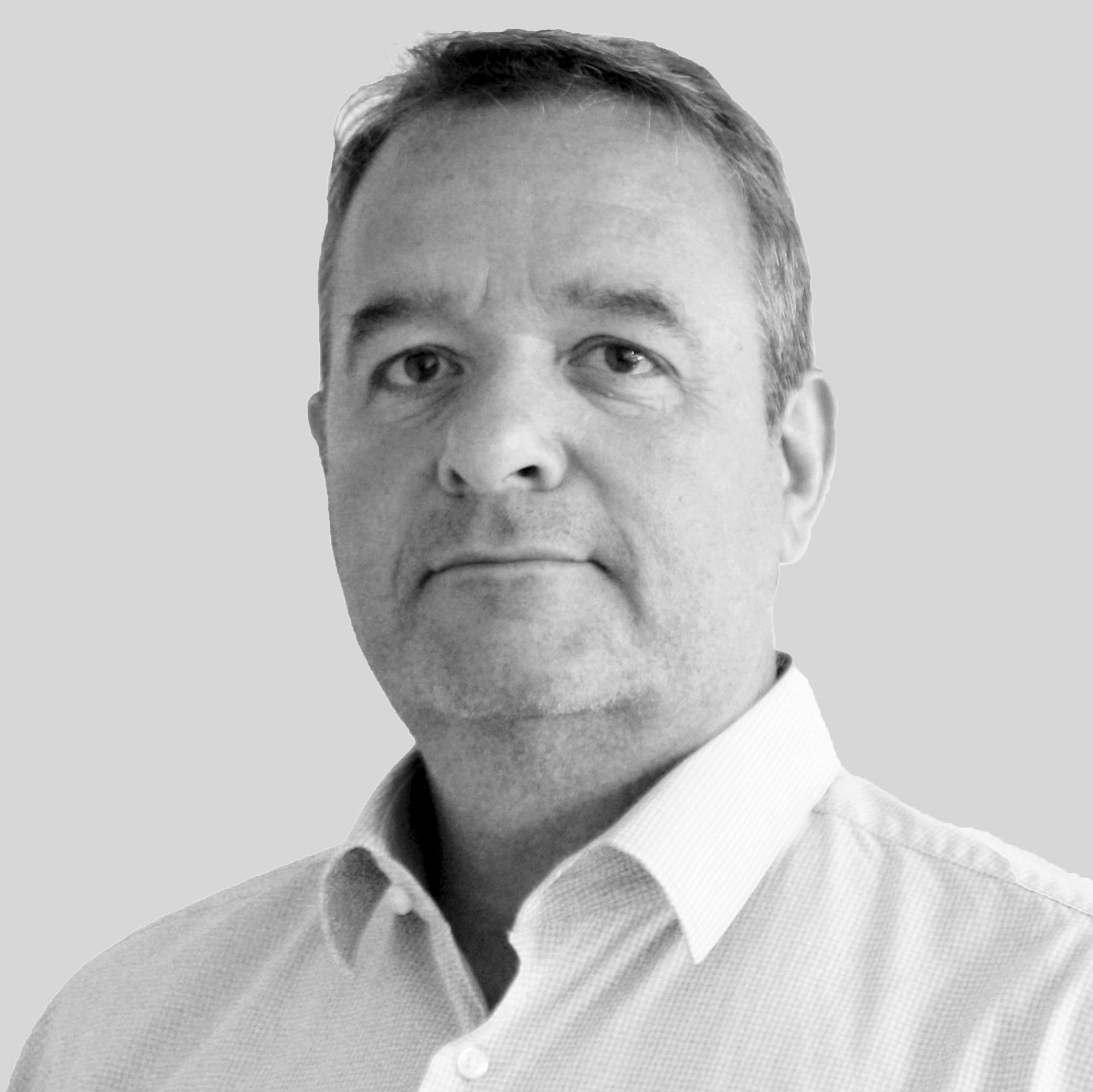
Two complete versions for long distances and curved advances
In addition to our all-rounder Gyro system, our expert system with LaserTotalstation support is available. This flexibility makes TUnIS Navigation MT unique. The navigation and advance process can thus be optimally coordinated, significantly reducing scheduled downtimes for calibration of the navigation system. Advances with small diameters benefit from the simplified, time-saving control surveys of the all-rounder Gyro system. The expert system TUnIS Navigation MTLaserTotalstation requires 50% fewer control surveys, significantly increasing the jacking performance for long-distance advances.
Steering with feeling
An integrated correction curve module assists the shield operator in steering the machine, when there are major unplanned deviations from the design position. The steadier, better-dosed steering of the machine has a positive effect on the jacking forces and the load on the pipes. The time-consuming use of intermediate jacking stations is reduced.
Increased operational safety
Vertical coupled navigation as an alternative calculation method for height determination
If TUnIS Navigation MTGyro’s hydrostatic water level fails, the advance can be continued by simply switching to the alternative calculation. At high advance speeds the alternative calculation stabilises the display of the vertical TBM position. The rate of advance no longer has to be reduced in order to obtain a stable reading.
Simple and uniform operating concept in all operating modes
The machine operator always works with the same familiar software interface. They’re able to find their way around the system faster and gain confidence in its use, thus minimising the risk of operating errors.
Quality assurance
Everything under control
Our system automatically records the actual position of the pipeline approximately 30 meters behind the TBM. By comparing this with the TBM position, the expert LaserTotalstation system evaluates the accuracy of the currently displayed TBM position. In this way, control surveys can be carried out in a more targeted manner and unpleasant surprises – such as large deviations from the design position after measurement – can be avoided. This increases assurance in the quality of the advance.
Predictive data analysis
TUnIS Navigation MT carries out a large number of redundant calculations in order to identify undesirable developments in the early stages of the jacking process and to ensure that the end position of the thrust pipes corresponds qualitatively to the project requirements. Alternative calculations monitor the performance of the electronic hydrostatic water level in the all-rounder Gyro system. In the expert LaserTotalstation system, the alternative calculations provide indications of floating thrust pipes.
An investment that pays off
The right solution for all your applications
The all-rounder Gyro system can be easily integrated into the tunnelling system – even those with very small diameters – and is also ideally-suited for open face machines and tight radii curves. The expert LaserTotalstation system enables high performance rates for long-distance advances. With the TUnIS platform, switching to segment tunnelling is easy and uncomplicated.
Equipped for the future
Progress for the entire product family
The TUnIS software platform is the basis for all VMT navigation systems. The microtunnelling systems benefit directly from developments and improvements in the other navigation systems – and vice versa.
Keep an overview
Permanent access to important KPIs, high data availability and practical tools for processing large amounts of data do more than ensuring maximum transparency. They are also becoming increasingly important in the steering of smaller tunnelling projects. An interface to our own data management system ensures that your data is in good hands.
Peace of Mind
Everything under control
TUnIS Navigation MT relies on a simple and uniform operating concept, so that incorrect operation can be largely avoided and the system routinely used after a short time. Our configuration assistant guides the user step-by-step through the system configuration, ensuring that all required settings are applied correctly. If questions arise during configuration, the assistant offers efficient support for quick troubleshooting.
-
Vertical coupled navigation ensures less dependency on the electronic hydrostatic water level with the following benefits:
a) The height calculation from the hydrostatic water level system is monitored
b) In the event of hydrostatic water level failure or malfunction, system navigation can continue (redundancy) -
The Chart Module offers:
• Immediate and clear analysis of the horizontal and vertical shield drive
• Direct comparison of the height calculation, using hydrostatic water level and coupled navigation
• Verifying control surveying quality through the import of measured comparison points and display in the chart - The navigation system can be used in any tunnelling from DN 800 upwards, even in lorry operation. It requires no line of site in the tunnel, no additional installation and is extremely compact in its design.
- Control surveying follows a simple scheme and can be carried out independently by the user after a short briefing.
Screenshots
![]() |
![]() |
![]() |
![]() |
- The „Quick-Check“ Option simplifies and speeds up the control surveying process, reducing downtimes and significantly simplifying system handling
- Alternative calculation methods such as vertical coupled navigation provide indications of floating thrust pipes
-
The system requires 50 % fewer control surveys than the all-rounder Gyro system
> Less interruption of tunnelling, shorter downtimes, increased tunnelling performance -
The automatically recorded actual position of the pipeline approx. 30 m behind the TBM is displayed – alongside the recorded TBM position – in the reference line editor, providing an indicator which evaluates the accuracy of the currently displayed TBM position
> Ensures less deviation from the design alignment, enables more precise steering and thus reduces the jacking forces – which, in turn, reduces the load on the pipes -
Additional measurement and control of the product pipe position 30-50 m behind the tunnelling machine
> Monitors and documents pipeline behaviour during advance, thereby ensuring its correct final position
Screenshots
![]() |
![]() |
![]() |
The optimal supplement for your long-distance and curved drive navigation systems
The MultiStation assistance system automates the control measurements required in microtunnelling projects to readjust the navigation systems used.
Microtunnelling navigation systems usually have to be calibrated at regular intervals. This is done by a classic, manual traverse measurement from the launch shaft through the pipeline to the machine. The manual traverse measurement typically requires the use of specialised surveyors and a standstill of the tunnelling machine for several hours.
The use of the MultiStation makes control measurements much more efficient: Tunnelling only has to be interrupted for a few minutes. Specialised surveyors need to be on site much less frequently.
- Reduction of downtimes for control measurements to a few minutes: Downtimes of several hours are no longer necessary, as is the case with manual control surveys.
- By automating the control measurements, there is no longer any need for a surveyor to be on site. This reduces the costs for services of surveying experts.
- Control surveys can be carried out at shorter intervals, at any time. This avoids larger deviations, reduces corrective steering to the minimum necessary and minimises both jacking forces and pipe loads: The quality of the pipeline is significantly improved.
- Control measurements can also be carried out for smaller diameters (down to DN 1200) – this means for pipes that cannot be entered. Thus, even long-distance and curved drives in these diameters can be excavated with high accuracy, resulting in considerable cost advantages during construction.
Screenshots
![]() |
![]() |
![]() |